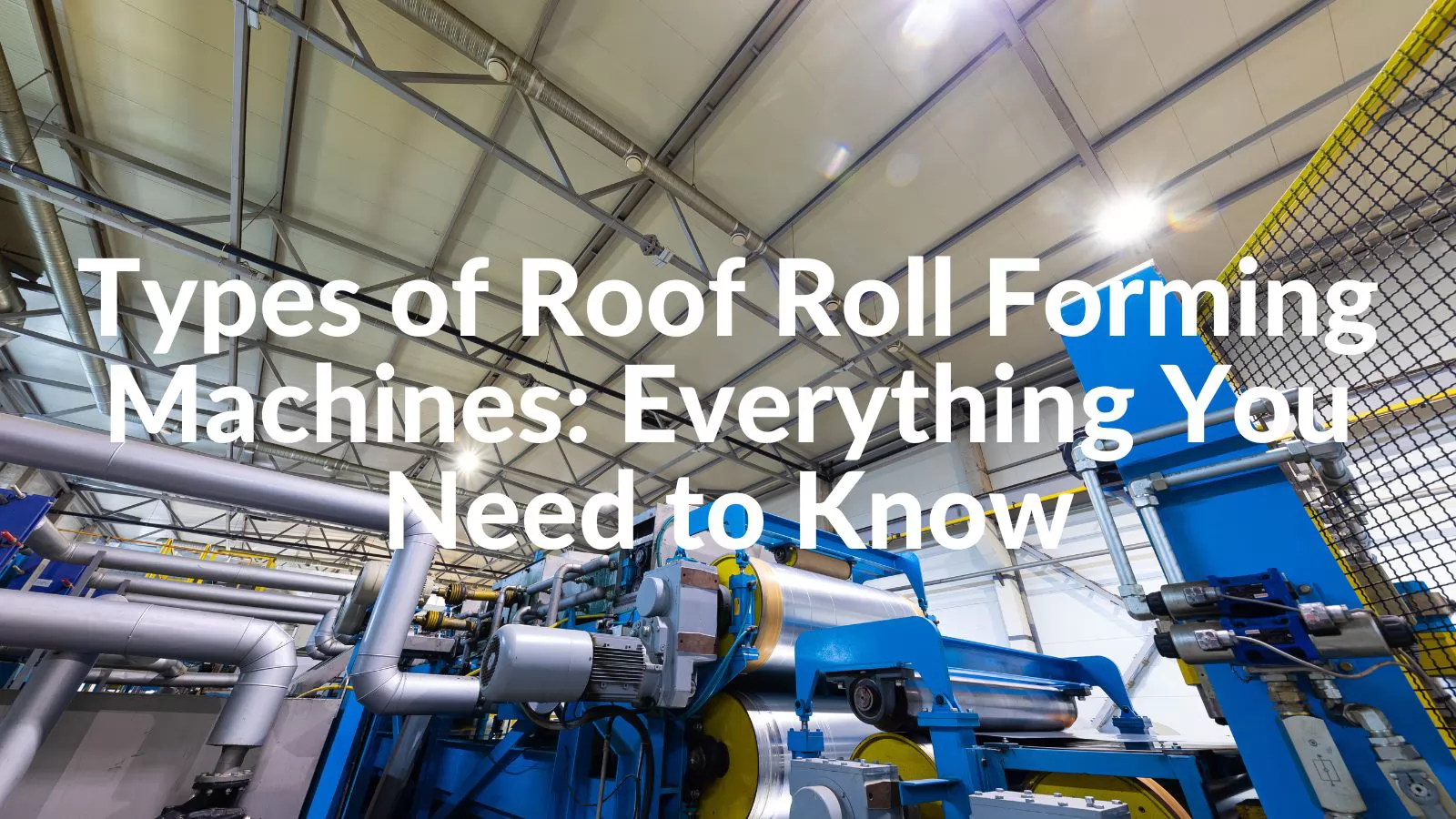
One technique that has revolutionized the industry when it comes to building durable and efficient roofs is the use of roof roll formers. These powerful machines are designed to transform raw materials into precisely formed metal roof panels in a variety of contours and shapes. Formetal will take an in-depth look at roof roll forming machines, exploring their types, features and the benefits they provide. Let us take actions!
What is the Roll Forming Machine Process?
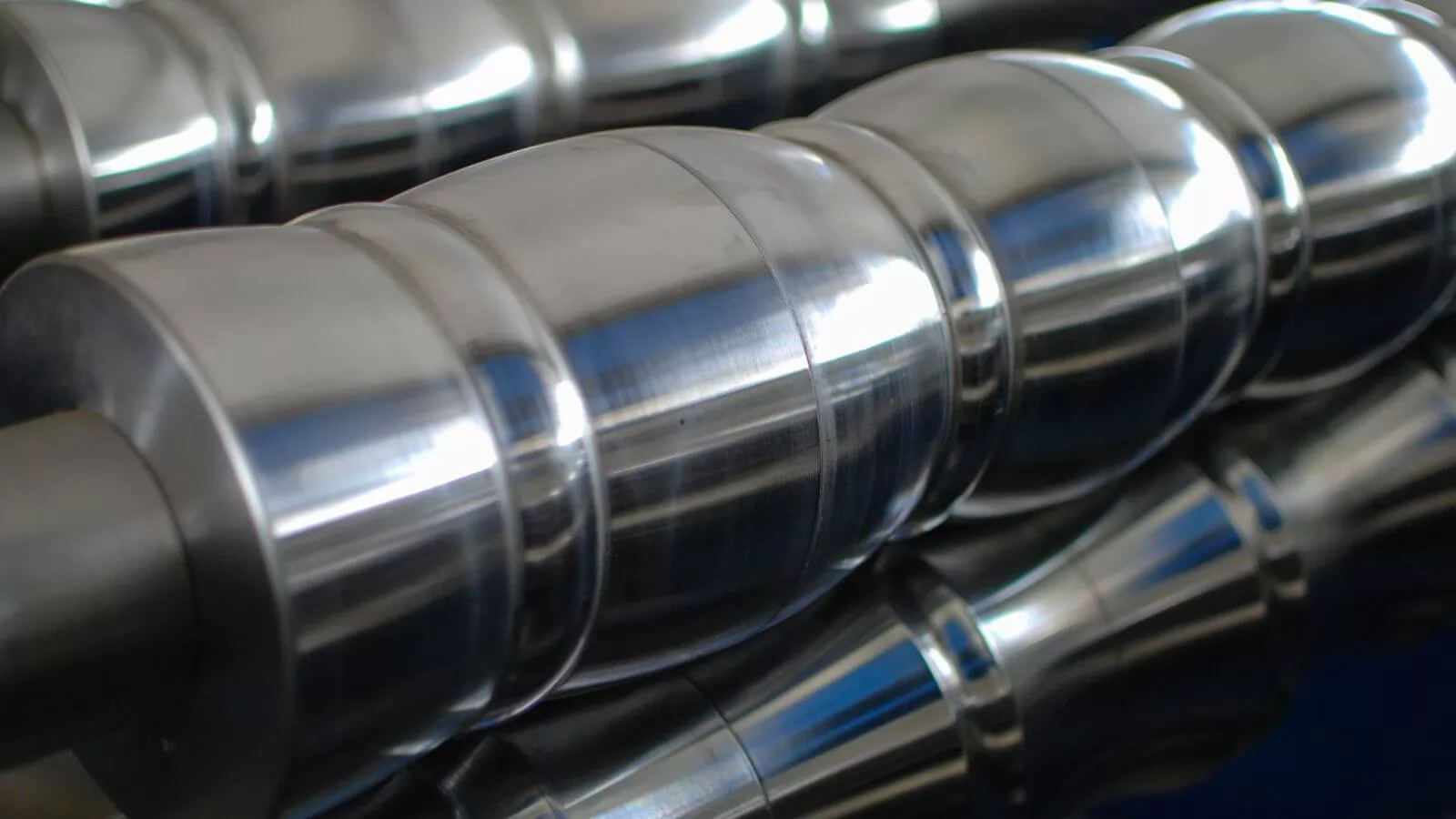
• Material Loading
• Pre-Cutting or Pre-Punching
• Roll Forming
• Cutting
• Post-Forming Operations
• Stacking or Packaging
More Details: How Roll Forming Machines Work
The roof panel forming machine is specially designed to meet different roofing needs and can produce various types of roof panels with specific profiles. Here are some of the most popular roof panel molding machines for reference.
1. Highspeed Roof Panel Roll Forming Machine
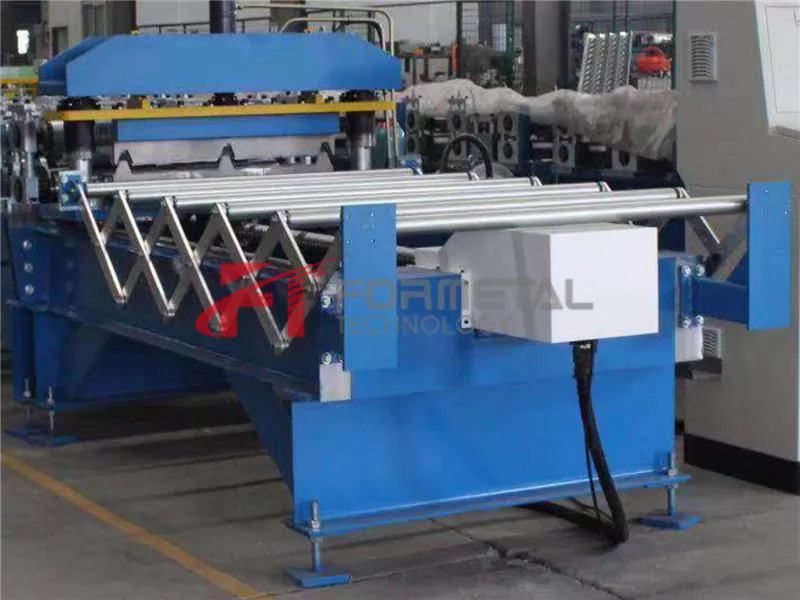
Highspeed Roof Panel Roll Forming Machine is the profiling line for roof panel with flying cutting. Compared with the normal roll forming machine, Highspeed Roof Panel Roll Forming Machine can continuously produce thesheet without stop. It consists of uncoiling system, guiding system, roll forming system, post servo cutting system(flying cutting), transfer roller, stacking system, electric system and hydraulic system etc.
2. Standing Seam Metal Roof Roll Forming Machine
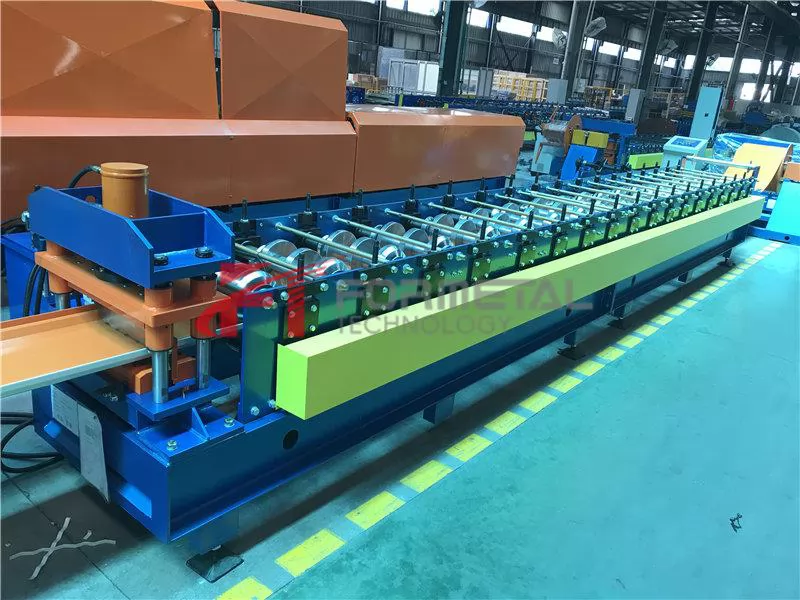
Standing Seam Metal Roof Roll Forming Machine is making the stand seaming roofing. It can continuous form the steel sheet according to customer’s requirement, automatically uncoiling, roll forming and cut to length. The machine can be put in a 40 ft container for easy transporting in the construction site. The roof should be seamed by automatic seamer during the installation.
3. Corrugated Roof Sheet Roll Forming Machine
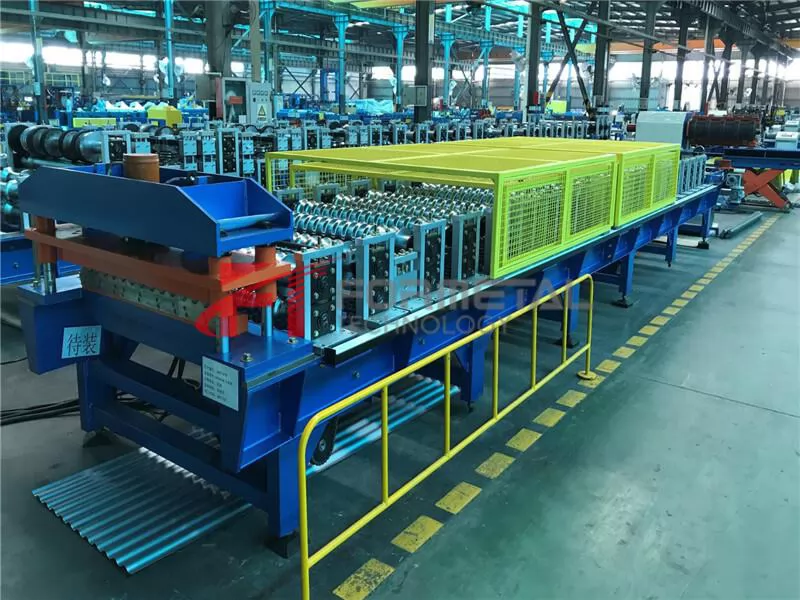
Corrugated Roof Sheet Roll Forming Machine is the special roll forming machine for steel sheet cold-form industries. It can continuous form the steel sheet according to customer’s requirement, automatically uncoiling, roll forming and cut to length. This equipment has many advantages, just like high forming speed, low noise, stable transmission, easy operation, good look and so on.
4. Sandwich Panel Roll Forming Machine
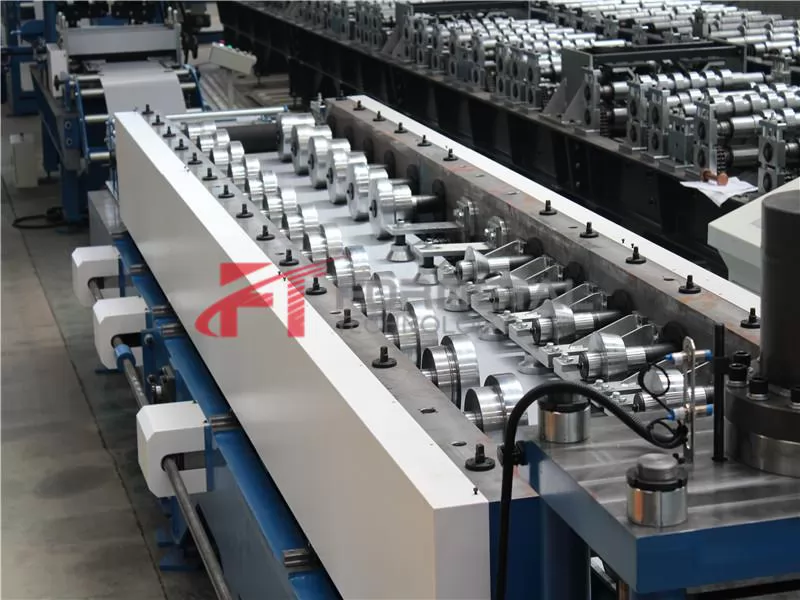
Sandwich Panel Roll Forming Machine is the rolling forming section of the sandwich panel continuous line. It’s producing the upper or lower metal layer of the sandwich panel. It can produce the wall or roof profile. The roll forming machine can be switched by moving on the rail for producing different profiles. It can automatically guide, micro ribbing and roll forming.
5. Glazed Roof Tile Roll Forming Machine
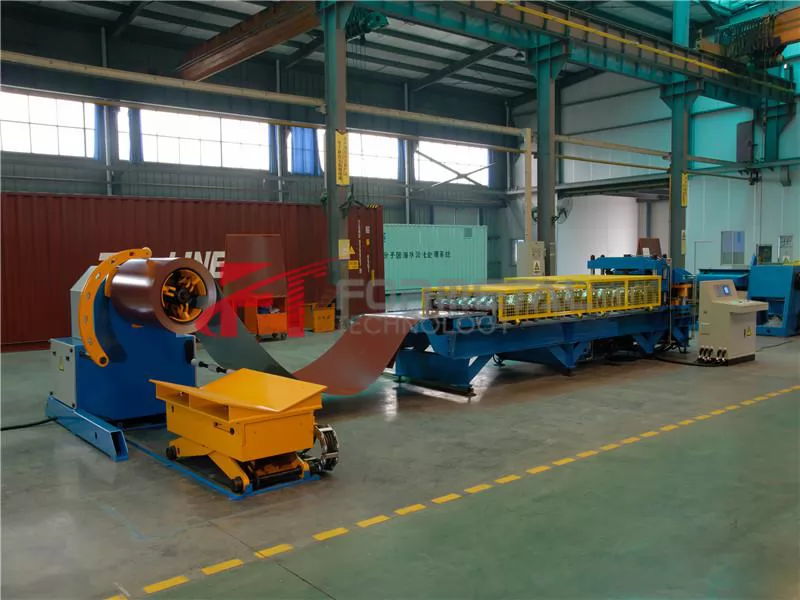
Glazed Roof Tile Roll Forming Machine (also named Step Tile Roll Forming Machine) is the special roll forming machine for steel sheet cold-form industries. It can continuous form the steel sheet according to customer’s requirement, automatically uncoiling, rolling, pressing and cut to length. This equipment has many advantages, just like high forming speed, low noise, stable transmission, easy operation, good look and so on.
6. Metal Roof Roll Forming Machine
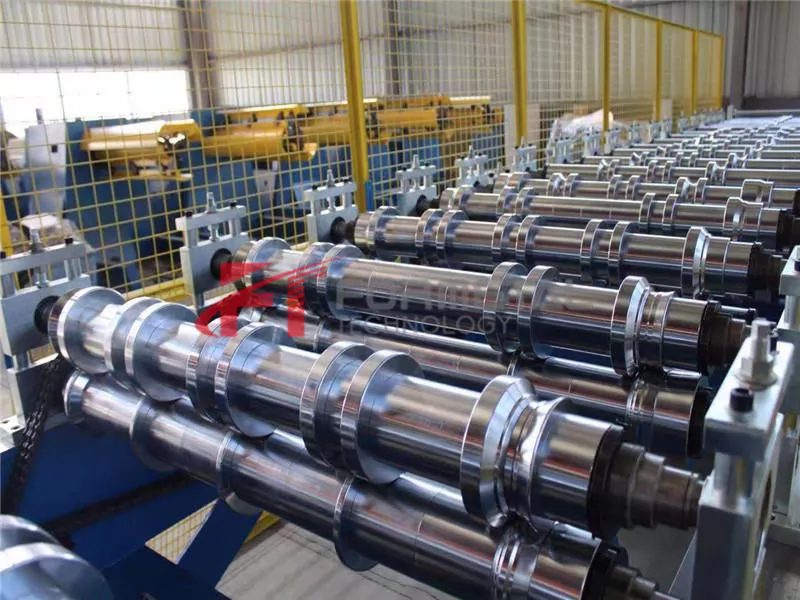
Metal Roof Roll Forming Machine is the special roll forming machine for producing the roofing sheet. It can continuous form the steel sheet according to customer’s requirement, automatically uncoiling, pre-cutting, roll forming and cut to length. This equipment has many advantages, just like high forming speed, low noise, stable transmission, easy operation, good look and so on.
• Precision and Consistency
• Increased Efficiency and Productivity
• Versatility and Customization
• Cost-Effectiveness
• Consistent Quality and Durability
• Streamlined Production Process
• Enhanced Safety
Maintenance and Care for Roof Roll Forming Machines
Proper maintenance and care are essential for ensuring the longevity, efficiency, and reliability of roof roll forming machines. Regular upkeep helps prevent breakdowns, extends the machine's lifespan, and maintains consistent production quality.
■ Follow Manufacturer's Guidelines
Always refer to the manufacturer's guidelines and instructions for maintenance procedures. The manufacturer's manual will provide specific information regarding maintenance schedules, lubrication points, and recommended spare parts. Adhering to these guidelines ensures that you follow the correct procedures and maintain the warranty validity.
■ Regular Cleaning
Keep the machine clean and free from dust, debris, and accumulated materials. Regularly remove dirt, metal shavings, and other contaminants from the machine's components, such as rollers, gears, and cutting blades. Clean the machine after each production run or as recommended by the manufacturer. Use appropriate cleaning tools and materials to prevent damage to the machine.
■ Lubrication
Proper lubrication is crucial for maintaining the smooth operation of the machine's moving parts. Follow the manufacturer's instructions for lubrication intervals and use recommended lubricants. Apply lubricants to the designated points, such as bearings, chains, gears, and sliding surfaces. Regularly inspect the lubrication system to ensure it is functioning properly.
■ Belt and Chain Tension
Check the tension of belts and chains regularly to ensure optimal performance. Improper tension can lead to slippage, misalignment, and premature wear. Follow the manufacturer's recommendations for proper tensioning techniques and adjust as necessary. Inspect the belts and chains for signs of wear, cracks, or damage, and replace them when required.
■ Calibration and Alignment
Periodically calibrate and align the machine to maintain accuracy and consistency in producing roof panels. Check the alignment of the rollers, guides, and cutting blades to ensure they are properly aligned and parallel. Make any necessary adjustments to maintain the desired dimensions and profiles of the roof panels.
■ Electrical and Safety Systems
Regularly inspect the electrical components, wiring, and safety systems of the machine. Ensure that all connections are secure and free from damage. Test the emergency stop buttons, safety sensors, and interlocks to verify their functionality. Address any electrical issues or safety concerns promptly to prevent accidents and ensure a safe working environment.
■ Spare Parts Inventory
Maintain an inventory of essential spare parts for the roof roll forming machine. Identify critical components that are prone to wear or failure, such as cutting blades, bearings, and sensors. Keep an adequate supply of these spare parts to minimize downtime in case of unexpected breakdowns.
■ Professional Maintenance and Servicing
While regular maintenance can be performed in-house, consider scheduling periodic professional maintenance and servicing of the machine. Professional technicians can conduct comprehensive inspections, perform complex repairs, and provide expert advice on optimizing the machine's performance.
Understanding the different types of roof panel roll forming machines, such as single profile, double layer, standing seam, corrugated, metal tile, trapezoidal, C/Z purlin, hidden fix, and step tile machines, allows manufacturers to select the most suitable machine for their specific needs.